Press Brakes | OEM Embedded Solutions
Tailored technology solutions for press brake manufacturers
Overview
Our OEM embedded solutions are designed to allow a high level of flexibility to meet the needs of individual press brake manufacturers. Unlike traditional component suppliers, we partner with press brake manufacturers to provide unique, tailored hardware and software solutions that are configured to suit any level of functionality, performance and price and personalised to suit the manufacturer’s exact requirements.
Through close technical collaboration, we assist in streamlining your press brake design and production process, enabling you to deliver machines with the highest level of functionality, productivity and performance to your customers.
Take control
A strong foundation is the key to developing a complete solution for your press brakes. The PCSS-A Series of embedded safety controllers provide you with the ideal platform to streamline press brake control and safety management for a more efficient, cost effective and flexible machine design.
Design comparison
PCSS-A Series controllers provide an efficient and cost effective platform with fewer components, reduced wiring, simplified interface and a CE Certified hardware / software combination that minimises your design and build times.
Tailored drive control
The PCSS-A platform simplifies machine drive control with dedicated hardware and a wide range of pre-configured or individually customised software modules to suit hydraulic, hybrid and electric press brakes.
Intelligent SmartLink << >> CNC Interface
PCSS-A SmartLink technology provides a seamless integration between key machine elements including the machine drive system, safety control, optical protection, optical imaging and the CNC system. This enables an intelligent flow of information that significantly enhances the operation, functionality, performance and efficiency of the press brake.
SmartLink manages synchronised control of the machine drive system, safety control, operator controls and the CNC system for more efficient and streamlined operation. Overall machine system status can be displayed on the CNC in real-time for an improved user experience.
SmartLink enables optical protection modes to be selected and customised in the CNC bend program. A different mode or combination of modes can be selected for each bend, allowing for streamlined bend programs that match the profile of the work piece.
SmartLink automatically switches modes on each step of the bend program with intelligent blanking of individual sensors to eliminate unnecessary stops and pedal presses for reduced cycle time and the fastest possible part production.
SmartLink displays diagnostic messages on the CNC screen to report machine conditions and faults in real time. SmartLink aids service personnel in quickly identifying and resolving machine faults to significantly minimise down time and get the machine back into production.
SmartLink brackets enable fully automated adjustment of the integrated protection system when paired with BendShield technology. The transmitter and receiver can be automatically raised and lowered according to the tools selected in the bend program without the need for any operator intervention. Advanced optical verification of the installed tools confirms that the machine is correctly configured, ensuring safe and error free operation.
When paired with BendVision technology, SmartLink manages the flow of image data to the CNC to enable advanced bending functions such as angle measurement, real-time angle control, active tool recognition and much more.
Next level safety with AutoSense technology
PCSS-A with AutoSense technology automatically monitors machine operation and performance in real-time. Everything including machine control commands, motion, direction, speed and stopping performance is automatically monitored in order to maintain a high level of machine and operator safety. AutoSense also guarantees compliance with international safety standards that require automatic monitoring of machine overrun and safe speed.
AutoSense Plus
AutoSense Plus provides additional monitoring to detect and diagnose specific machine electrical and hydraulic faults with visual alerts displayed on the CNC via SmartLink. Machine problems are quickly and easily identified to get your machines back into production with minimal downtime.
AutoSense Ultimate
AutoSense Ultimate adds advanced Dynamic Valve Monitoring technology to automatically monitor hydraulic valves, associated control commands and machine actions. Dynamic Valve Monitoring reduces machine build cost and complexity by eliminating the need for separate monitoring systems and monitoring sensors built into the hydraulic valves.
Wireless Foot Pedal Technology
The wireless foot pedal solution is an expansion option for the PCSS-A1 or PCSS-A2 platform that makes it easy to incorporate wireless functionality into your machines with flexibility to integrate the wireless module into your existing foot pedal or designing a new pedal from the ground up.
Optical Protection
Overview
Integrated optical protection has never been simpler and with a wide range of options available, your press brakes can be configured with the perfect balance of safety and performance versus cost to suit any market level. Each optical protection solution comprises a laser transmitter and receiver set that simply interface to your PCSS-A controller. Functionality and operation is embedded and automated within the CNC via SmartLink technology for a seamless and efficient guarding solution.
Close proximity operation
Optical protection systems comprise a laser transmitter and receiver that are mounted to the upper beam of the press brake. A continuous laser field protects the zone around the punch tip allowing the operator to hold the work piece as the tools close at high speed. If an obstruction is detected the machine is automatically stopped.
This close proximity protection allows the operator unrestricted access to the point of operation for increased productivity and unlike traditional light curtains, reduces operator fatigue by eliminating the need to continually move in and out of the operating area.
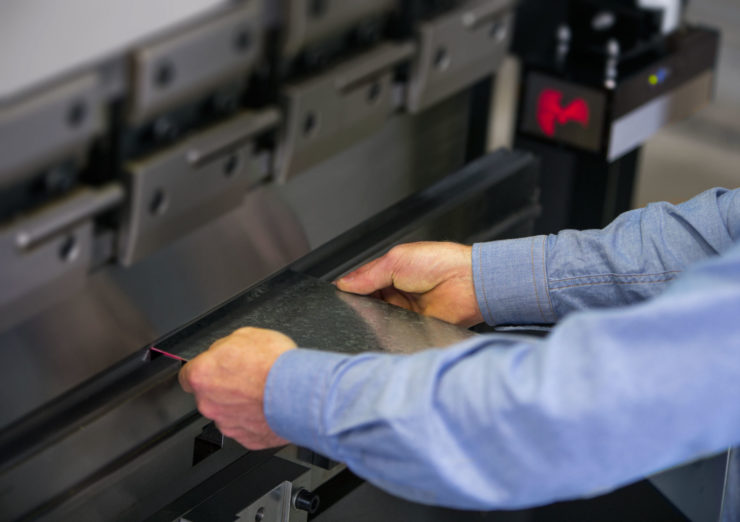
Sensor arrangement
The laser field is processed by the receiver and divided into three continuous zones to detect obstructions entering from the front, sides and rear of the tool area. The front zone provides protection forward of the tool while the middle zone protects the area just behind the tip of the punch. The rear zone provides additional protection for the open gaps created when segmented tooling is used. The protective zones are independently and automatically muted to suit different shaped work pieces allowing parts to be formed safely at high speed to achieve maximum productivity.
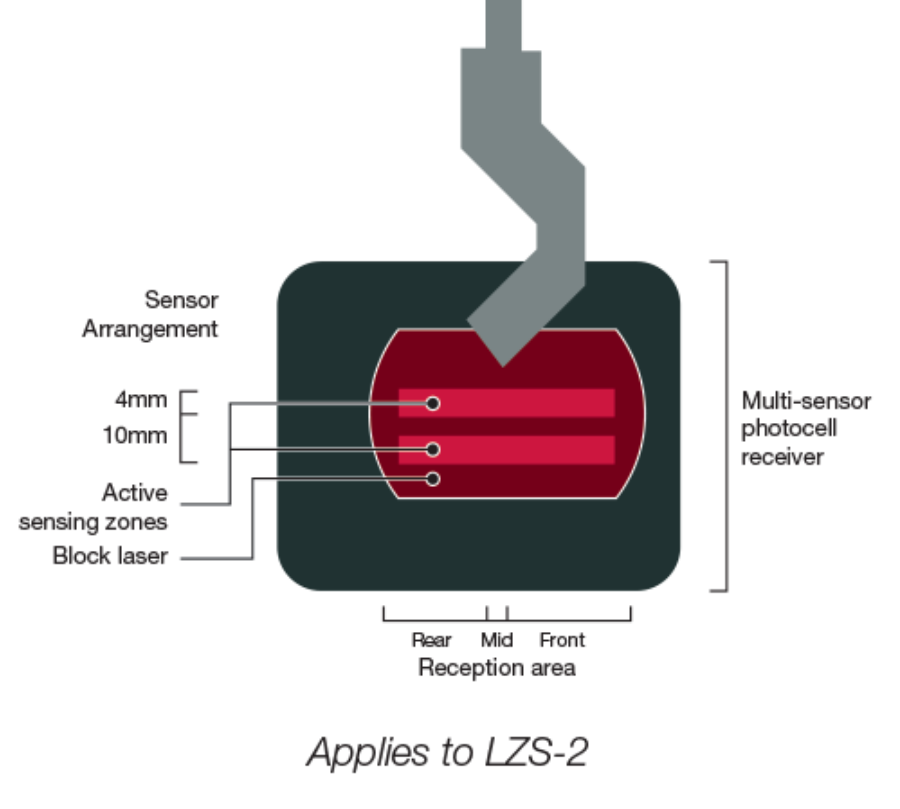
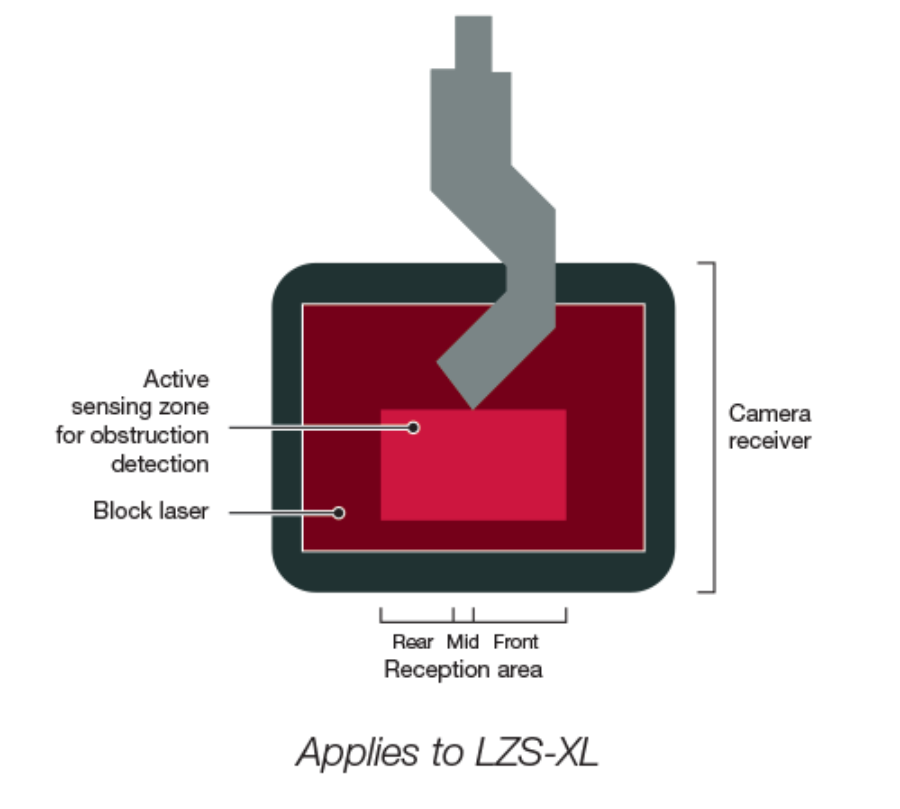
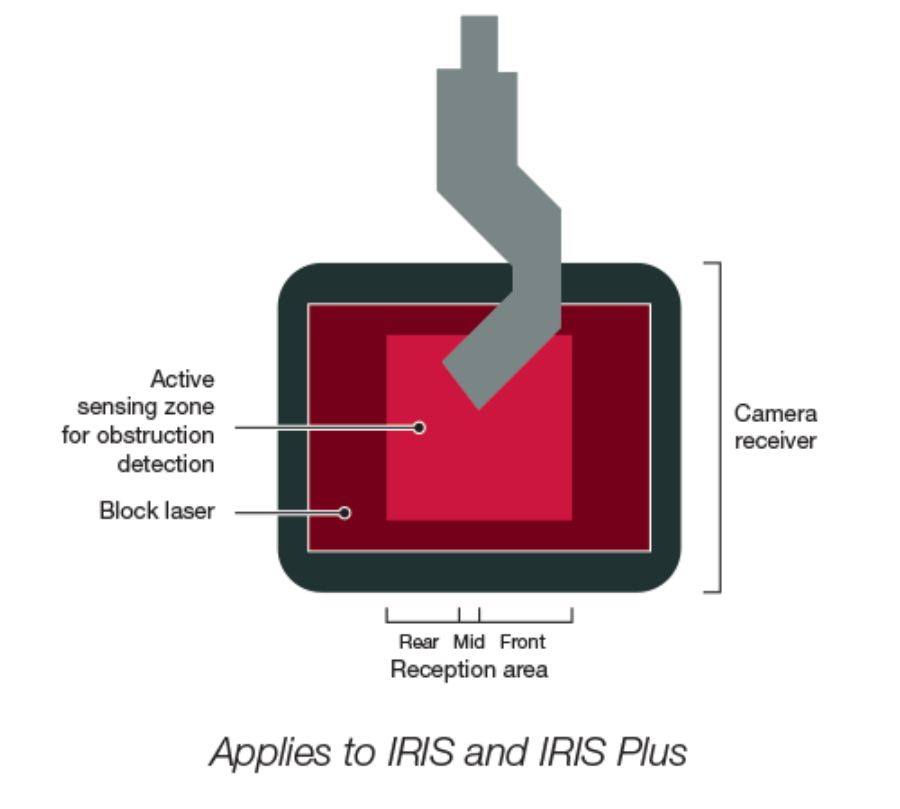
Advanced optical protection
BendShield dynamic sensing technology provides an advanced level of optical tool protection for press brake operators by enveloping the punch tip with a protective field that has no gaps while maintaining high-speed operation. With a detection capability of 6mm, BendShield detects obstructions from any angle. Press brakes with BendShield technology are not only the safest but also the most productive with guaranteed levels of safety and high-speed performance.
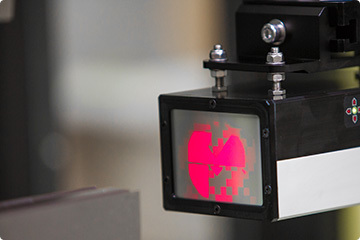
BendShield features
Advanced functions
Every second counts
RapidBend Ultimate technology changes the game by enabling press brakes to operate without restriction to achieve maximum safety and performance. Through a high-speed dynamic muting process and in conjunction with BendShield technology, the tools can close safely at maximum speed, then transition to bending speed right at the material pinch point. This effectively reduces the speed change point to 0mm, eliminating unnecessary slow speed travel to minimise the machine cycle time. RapidBend Ultimate works with a wide range of part profiles including box bending with side flanges.
With time savings of as much as 3 seconds per cycle, RapidBend Ultimate boosts machine performance to significantly enhance your productivity.
The ultimate solution for tandem press brakes
The PCSS-A platform expands the possibilities for machine control with the next generation solution for tandem press brakes. Our advanced Tandem Adaptor synchronises safety functions and control across both machines and paired with a dedicated optical system for flexible guarding in both single and tandem configurations.
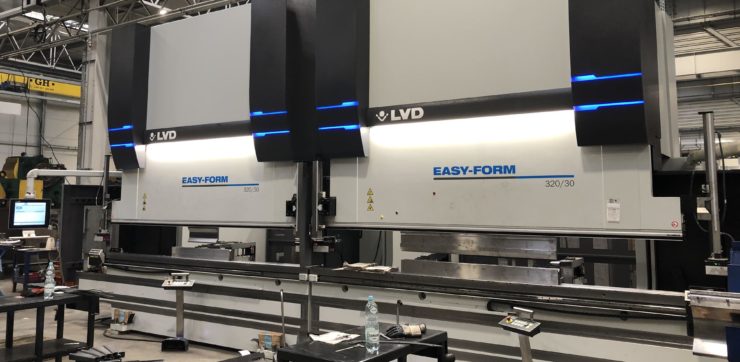
IRIS Optical Imaging Technology
IRIS and IRIS Plus optical systems incorporate an integrated real-time image processor that is contained within the receiver unit. Our optical imaging technology provides greater flexibility for press brake manufacturers by combining high-performance optical protection with real-time image processing capabilities.
As combination systems, both IRIS and IRIS Plus models provide high- performance optical protection while the tools are closing at high speed, then once the bending process starts, the image processing functions take over. During bending, the systems take and process images in real-time and transfer live data to the CNC system via SmartLink. As the image data processing system is completely contained within the IRIS and IRIS Plus receivers, no additional processing hardware or software is required.
IRIS and IRIS Plus optical imaging is a flexible technology platform that allows press brake manufacturers to utilise the real-time image data to develop and implement a wide variety of advanced functions and processes in the CNC system. The optical imaging technology requires supporting CNC system software that is co-developed and customised for each manufacturer.
Bend Speed Management
Bend Speed Management facilitates higher bending speeds in excess of 10mm/s when using wider V-dies. IRIS and IRIS Plus systems process real-time images of the bending process to calculate the angular velocity of the moving sheet and measure the speed at which the part is being formed. Faster bending speed is possible when the angular velocity is less than 135 degrees per second.
BendVision technology
BendVision is an extension of our image processing technology that provides real-time analysis of the bending process. The technology is incorporated into the existing hardware of the IRIS Plus optical guarding system so that no extra components are required, resulting in an efficient and cost-effective solution for press brake manufacturers.
BendVision concept
BendVision processes images of the press brake tools and material during the bending process and transfers a range of information to the CNC via SmartLink including raw and processed images as well as live angle data during bending. The press brake manufacturer can use real-time BendVision data to enable a wide range of customised functions and processes. These functions and processes are co-developed with Lazer Safe and the press brake manufacturer.
BendVision for angle measurement
BendVision technology provides a range of real-time angle measurement data that includes the inside and outside angles of the material, average angle, material warp angle, material spring back angle for various material types, thickness and grain direction, plus end of relaxation angle once the bend has been completed.
BendVision for angle control
The ability for the CNC to receive BendVision angle data opens up a wide range of possibilities for real-time angle control. Instead of just confirming angles are within tolerance, the CNC can use the live angle plus a measured spring back angle to control the bending depth for flexible active and dynamic angle control solutions.
Mounting Bracket Solutions
We offer a range of mounting bracket solutions for attaching the laser transmitter and receiver to the press brake. Standard and custom sizes are available to suit various machine types, machine lengths and optical configurations.
Standard brackets
Our Standard Brackets are manufactured from an extruded high-tensile alloy for
rigidity and tolerance to machine vibration with linear rails and bearings that provide
precision vertical adjustment of the laser transmitter and receiver. During tool change
a spring loaded locking pin keeps the transmitter and receiver clear allowing the tools
to be easily removed from the ends of the machine.
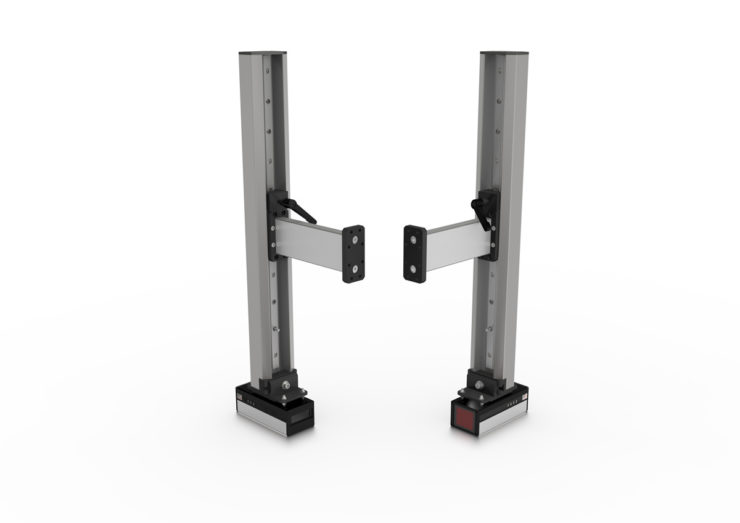
SmartLink Brackets
Available with IRIS and IRIS Plus systems, SmartLink Brackets automate the process of adjusting and positioning the transmitter and receiver during tool change. The SmartLink Brackets incorporate a compact motorised drive system that is interfaced with the CNC system for completely automated or simple one-touch operation.
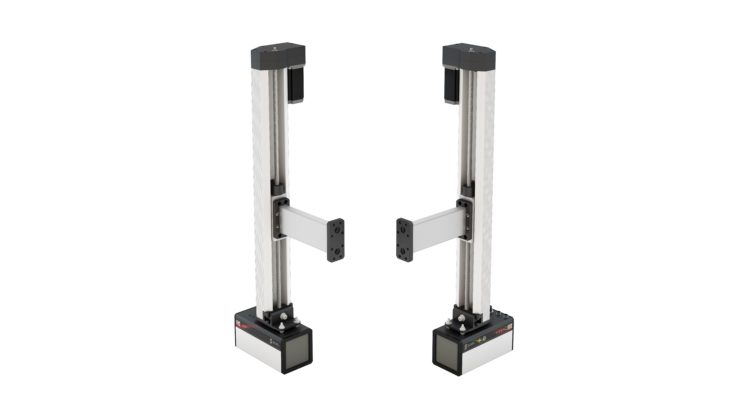
Press brakes with ATC systems
For press brakes with automatic tool changing systems, SmartLink Brackets offer the ultimate solution for completely automating the entire tool change process, eliminating the need for any operator interaction. When automatic tool change is initiated, the SmartLink Brackets can automatically move to a clear position for tool unloading / reloading and when tool change is complete, can automatically move to the new punch position, ready for the operator to start the next job.
Specifications
PCSS-A0 Plus | PCSS-A1 | PCSS-A2 | ||
---|---|---|---|---|
Technology | ||||
SmartLink | ||||
FlexSpeed | Plus | |||
AutoSense | Ultimate | Ultimate | Ultimate | |
Specifications | ||||
Safety inputs | 12 | 16 | 16 | |
Safety outputs | 4 | 6 | 6 | |
Standard inputs | 24 | 28 | 28 | |
Standard outputs | 6 | 10 | 10 | |
Linear encoder I/O | 2, both Y1 and Y2 | 2, both Y1 and Y2 | 2, both Y1 and Y2 | |
Minimum encoder resolution | 0.1 micron | 0.1 micron | 0.1 micron | |
Speed capacity of the encoder counters | > 300mm per second | > 300mm per second | > 300mm per second | |
Response time (hardware interrupts) | <1ms | <1ms | <1ms | |
SD Card (back-up, data logging and high-speed software transfer) | - | - | ||
CAN Open | - | - | ||
Ethernet | - | |||
EtherCAT | - | - | OPTIONAL | |
Dimensions | 229mm x 189mm x 45mm | 229mm x 189mm x 45mm | 229mm x 189mm x 57mm | |
Expansion Options | ||||
Tandem Adaptor | - | |||
SmartLink Brackets | - | |||
Wireless Foot Pedal | - | |||
Optics Compatibility | ||||
LZS-2 | ||||
LZS-XL | - | |||
IRIS / IRIS Plus | - | |||
Third party light curtain support | ||||
Dual guarding support |
LZS-2 | LZS-XL | IRIS | IRIS Plus | ||
---|---|---|---|---|---|
Optical protection functions | |||||
Optical imaging functions | - | - | |||
Laser transmitter | CLASS 1M | CLASS 1M | CLASS 1M | CLASS 1M | |
Receiver type | Multi-sensor photocell | Camera | Camera with integrated Intel® image processor | Camera with integrated high-speed Intel® image processor | |
Maximum recommended optical range | 8 metres | 15 metres | 8 metres | 4.5 metres | |
Minimum object resolution / Detection capability | 4mm / 14mm | 9mm / 14mm | 2mm / 6mm | 2mm / 6mm | |
Connector type | M12 8 pin | M12 12 pin | M12 12 pin | M12 12 pin | |
Tool compatibility | V tools and non-standard tools | V tools and non-standard tools | V tools and non-standard tools | V tools and non-standard tools | |
Integrated status LEDs | |||||
Special Functions | |||||
Automatic tool alignment | - | - | |||
Automatic alignment confirmation | - | - | - | ||
Special tools mode | - | - | |||
Soft stop mode | - | - | |||
Fast flattening mode | - | - | |||
Automatic Cycle Start (ACS) | - | - | |||
Bend Speed Management (BSM) | - | - | |||
Adaptive Environment Sensing (AES) | - | ||||
Technology | |||||
RapidBend | - | - | - | ||
RapidBend Ultimate | - | - | |||
BendShield | - | - | |||
BendVision | - | - | - | ||
Performance // Minimum speed change point | |||||
Flat sheet bending | 4mm | 3mm / 10mm | 0mm | 0mm | |
Box bending | 4mm | 3mm / 14mm | 0mm | 0mm | |
PCSS-A Series Compatibility | |||||
PCSS-A0 Plus | - | - | - | ||
PCSS-A1 / PCSS-A2 | |||||
PCSS-A Tandem Adaptor | - | - | - | ||
Mounting Bracket Compatibility | |||||
Standard Brackets | |||||
SmartLink Brackets | - | - |
IRIS | IRIS Plus | |
---|---|---|
Optical protection functions | ||
Optical imaging functions | ||
Maximum recommended optical range | 8 metres | 4.5 metres |
Optical sensor | ||
Camera | Digital Image Sensor | Digital Image Sensor |
Frame rate / frequency | 17ms / 59Hz | Selectable 5ms / 200Hz or 10ms / 100Hz |
Data resolution (sensor) | - | 0.01 degrees |
Measurement technology | ||
Type | Integrated Intel® image processor |
Integrated high-speed Intel® image processor |
Memory depth | - | Records up to 10 seconds (2000 images) of bend data per cycle |
Measurement accuracy | - | Up to +/- 0.25 degrees |
Measurement rate synchronised with frame rate | - | Selectable 5ms / 200Hz or 10ms / 100Hz |
Imaging technology | ||
Bend Speed Management | ||
BendVision | - |
Standard | SmartLink | ||
---|---|---|---|
Specifications | |||
Vertical bracket length | 520mm / 700mm / 1000mm | 550mm / 700mm / 1000mm | |
Vertical adjustment range | 350mm / 530mm / 830mm | 350mm / 500mm / 800mm | |
Horizontal adjustment range | 40mm | 40mm | |
Maximum recommended machine length | 15 metres | 6 metres | |
Main Features | |||
Precision linear bearings and rails | |||
Free sliding operation | |||
Automatic motorised drive system | - | ||
Maximum speed of the motorised drive system | NA | 20mm/s | |
Adjustable locking handle | NA | ||
Tool change lock | Manual | Automatic | |
Optics Compatibility | |||
LZS-2 | - | ||
LZS-XL | - | ||
IRIS / IRIS Plus |
Get started
Ready to take the next step? Our OEM Embedded Solutions are available to press brake manufacturers that seek a standardised long-term solution with a technical partnership to develop and enhance the overall design of their machines.
Our Partner Program
Our OEM Partner Program goes far beyond the normal scope of supplying products and services. We establish close technical and business relationships in order to develop a long-term partnership with each manufacturer which enables us to deliver and maintain the best and most up to date technology solutions. We work together with our partners to continually develop and evolve technology to meet the ever-growing safety and performance requirements of press brake users.
Discover the benefits of our OEM Platinum Partner Program
Contact Us
If you are a press brake manufacturer and would like to learn more about our OEM Embedded Solutions, please contact us for a consultation.