However, for the most part, press brakes are still manually operated machines that require trained and skilled operators to achieve safe, efficient, and productive bending. Aside from bending parts, press brake operators are required to manage the setup and configuration of the machine safety and guarding devices and systems. An incorrect, or poor setup can not only result in a potential reduction in safety function but can also lead to a significant reduction in machine efficiency that results to lower productivity.
A press brake with an automated safety and guarding solution eliminates the need for manual adjustments to be performed by the operator by automatically driving the optical components to the correct position, then automatically making any necessary adjustments based on the tooling that had been installed. In addition, secondary processes automatically check and confirm the positioning and setup, thereby ensuring that the machine is always safe to operate.
The team at Lazer Safe, who are the industry leading specialists in the field of press brake safety and guarding solutions, are improving the way in which machine operators interact with the press brake through more advanced levels of Autonomous Guarding technology. Lazer Safe is leading the industry in Autonomous Guarding and have defined five levels of automation ranging from Level 0 through to Level 4.
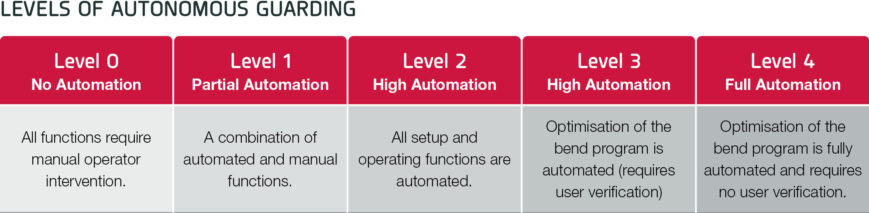
Press brakes designed to Level 0 essentially offer no automation, and therefore completely lack any automatic functions. The safety and guarding system and processes that are integrated with the machine are purely manual and rely solely on the machine operator for any adjustment, setup, and alignment of the guarding system, plus safety performance testing and mode selection. This generally applies to press brakes that are designed and manufactured to achieve a lower cost or supplied into economy markets.
Level 1 progresses to low automation, where we start to see the introduction of press brakes with automatic functions such as automatic verification of the optical sensor position to the upper tool, verification of the tool height and material thickness, plus automatic guarding mode selection for each step in the bend program. This typically requires the press brake manufacturer to adopt integrated functions where processes are embedded in the CNC system software to facilitate more streamlined and user-friendly operation.
Press brakes designed with Level 2 Autonomous Guarding take a larger step forward to where all the of the safety and guarding setup, adjustment and operating functions are now automated. This presents the ideal solution where the operator turns on the machine, installs the tooling and starts bending parts – all without have to setup, adjust, or check any of the safety and guarding functions, and provided that the bend program has been optimised, there is very little to no interference when forming parts.
Streamlined configuration and optimisation of the bend program can eliminate or drastically minimise interference with the sensing zone, which results in fewer pedal presses, no unnecessary stops in the bending cycle and significantly more time in high-speed, resulting in faster and more efficient production. The only part of this process that is not automated (at Level 2), is optimisation of the bend program, which requires a higher level of automation.
Press brake manufacturers are already offering machines designed with Level 2 Autonomous Guarding, which has been widely available for around the past 5 years, and this has already driven positive results for the sheet metal industry.
Optimisation of the safety and guarding functions within the bend program is a significant factor that determines the true productivity output of the machine. If the bend program is not optimised, or is poorly configured, then this can result in an increase in cycle times and therefore a reduction in the number of parts produced per hour.
Without optimisation, we see several factors that impact productivity since there is no synchronisation between the guarding system’s optical sensing zone and the part profile. The effects of this are amplified when bending more complex parts that comprise multiple steps with side flanges. The lack of optimisation results in interference between the optical sensing zone and the work piece, that requires the operator to make additional pedal presses either before or during each cycle. In addition, there is often an increase in the slow speed travel distance before the upper tool reaches the material.
If the bend program is optimised, then the optical sensing zones are dynamically and automatically managed according to the part profile. Not only that, but the configuration of the bend program is optically verified against the physical part profile to ensure a higher level of safety. When starting a new job, the machine operator only needs to change the tools, start the bend program, then begin bending parts immediately. The addition of an Automatic Tool Changer in combination with Autonomous Guarding (Level 2 or above) eliminates another manual process and improves efficiency even further.
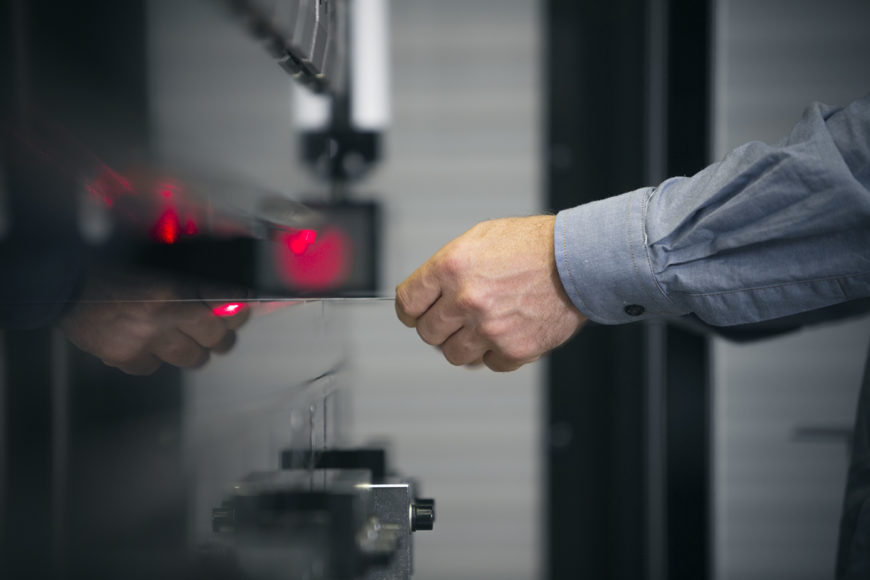
Currently with Level 2 automation, press brake operators and CNC programmers, are required to manually configure and optimise the safety and guarding functions in the bend program. This process involves analysing the part profile as is changes from one program step to the next, then selecting the most efficient guarding mode, or combination of modes, as well as inputting the parts dimensions such as the height of side flanges. Provided that the bend program is optimised correctly, then maximum efficiency and production output can be achieved.
Feedback from the sheet metal industry consistently identifies a common issue with this optimisation process, is that press brake operators may not always receive the necessary information or training. This is compounded due to frequent turnover of machine operators, or when experienced operators leave, taking valuable knowledge and skills with them. Another issue is the general shortage of skilled sheet metal workers which continues to present a challenge for employers.
To address these issues, Lazer Safe has identified the next stage of automation, with a transition to Level 3 Autonomous Guarding. This represents a significant development in press brake efficiency and productivity that was previously not possible.
Level 3 automation introduces a new process where the safety and guarding system in collaboration with the CNC system, share information to automatically learn the part profile and determine the optimal modes and settings for each step of the bend program. This takes the manual process and decision making out of the operator’s hands, saving time, and ensuring that bend programs are always optimised for maximum bending efficiency.
The learning process is automatically activated when a new bend program is run for the first time, and active only when the first part is formed. As each bend is processed, part profiles are optically detected, and the CNC displays a message to the operator confirming the optimal mode and parameter settings that will be automatically applied to each step of the bend program. Once the first part is completed, the bend program is now optimised, and the settings are automatically saved in the CNC. All subsequent parts can then be formed with maximum efficiency. Since the bend program is now optimised and settings automatically saved, the learning process does not need to be repeated the next time the operator runs the same program.
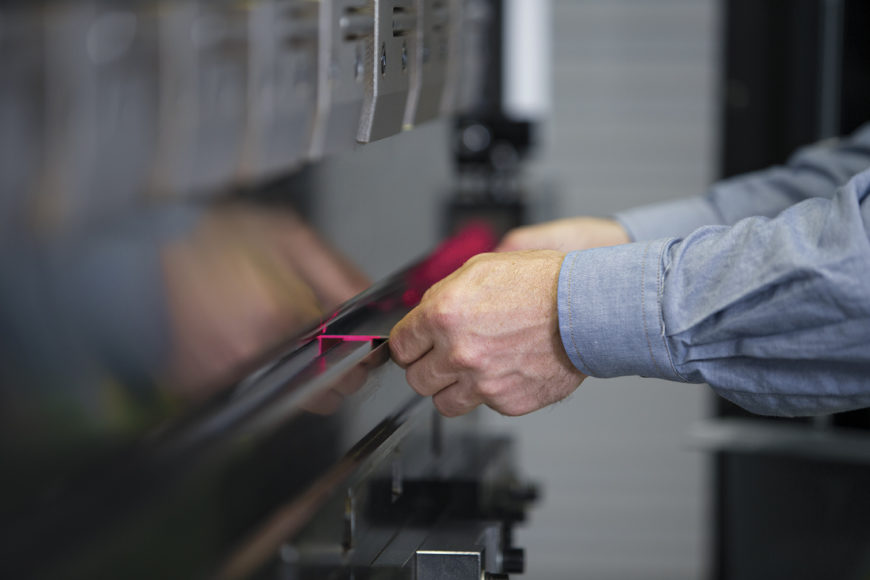
Level 4 Autonomous Guarding takes optimisation a step further, where software analyses the bend program and part profile in 3D, then automatically determines and applies mode and parameter settings without the need for a learning cycle. Level 4 is a more advanced process that will evolve over time, as Lazer Safe continues to drive innovation for the press brake industry.
Users that currently own and operate press brakes with Level 2 Autonomous Guarding are already realising the benefits of reduced setup times, less reliance on machine operators, and improved machine efficiency. The transition to Level 3 Autonomous Guarding will offer users even greater levels of productivity.
Many of the industry’s leading press brake manufacturers are already in the process of implementing Level 3 Autonomous Guarding and Lazer Safe anticipates rapid market adoption of this technology over the coming months.